When I’m ready to “make things permanent”, I start mixing / pouring the resin. After that, I spend a couple of hours tending it to ensure no ugly bubbles form on the finished surface and to decorate a bit more. Tending the resin equates to blowing it with a heat gun and moving things around with wooden pokers, as well as wiping up any excess (especially around the edges) with a sponge on a stick. I remembered to elevate this piece so I wouldn’t have the pain of removing the paper again.
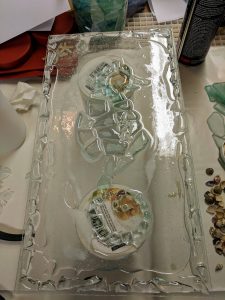
Above: Just poured. Below: after a once over with the heat gun.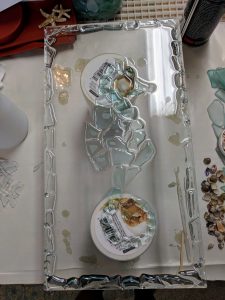
Below: Finishing the decorative details (shells, glass frit, glass chips, etc). Also making minor adjustments to positioning.
Now it just has to sit for a couple of days to cure, then I will clean up any drips, etc from the sides / back and get a better photo.