View pieces I have on hand available for sale at this link: https://sherryglaab.com/?page_id=2255
It’s been several months since I poured any resin, so I thought it would be a good idea to test out my resin on some smaller projects before I try it on the big Frank Lloyd Wright window. Some of my resin hardener has yellowed, so I had to toss it. Technically I could use it for projects that have pigments added to the resin, but I don’t want to chance it since most of my projects need clear resin. I had a batch on hand that hadn’t yet been opened, so I used that on these two Rainbow Rows that I made prior to beginning work on the big window. Luckily the temperature in my work area is at the ideal (75 degrees F) for resin right now.
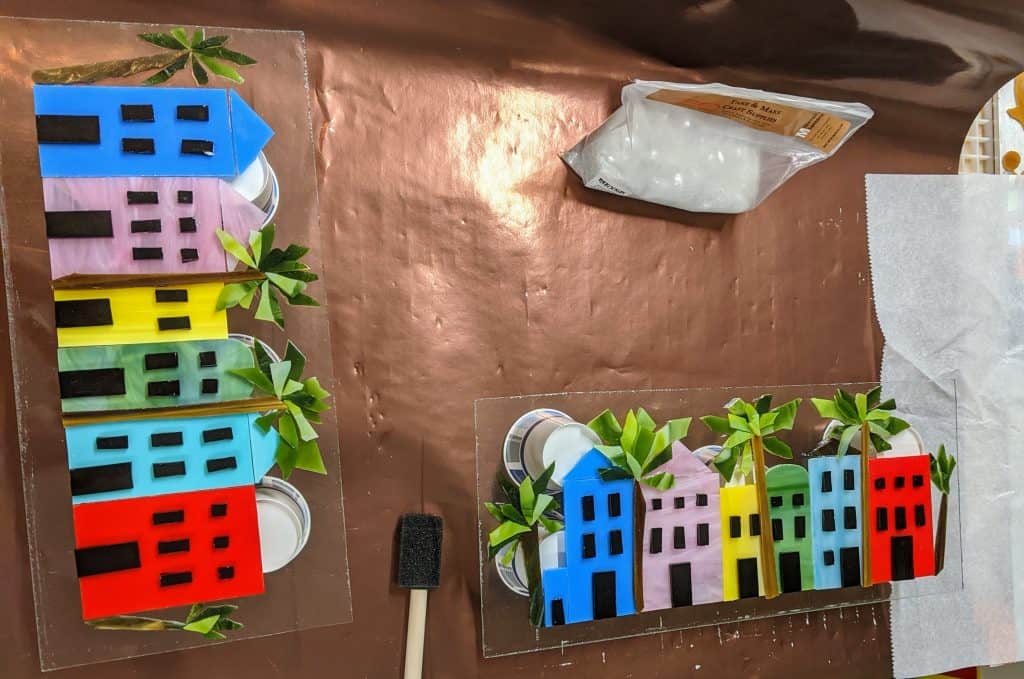
I meant to mix up about 8 ounces or resin, which is too much, but I can always make a couple of ornaments or coasters with the extra. I ended up overpouring and had 12 ounces to use up, so I made some ornaments and a big mess, too.
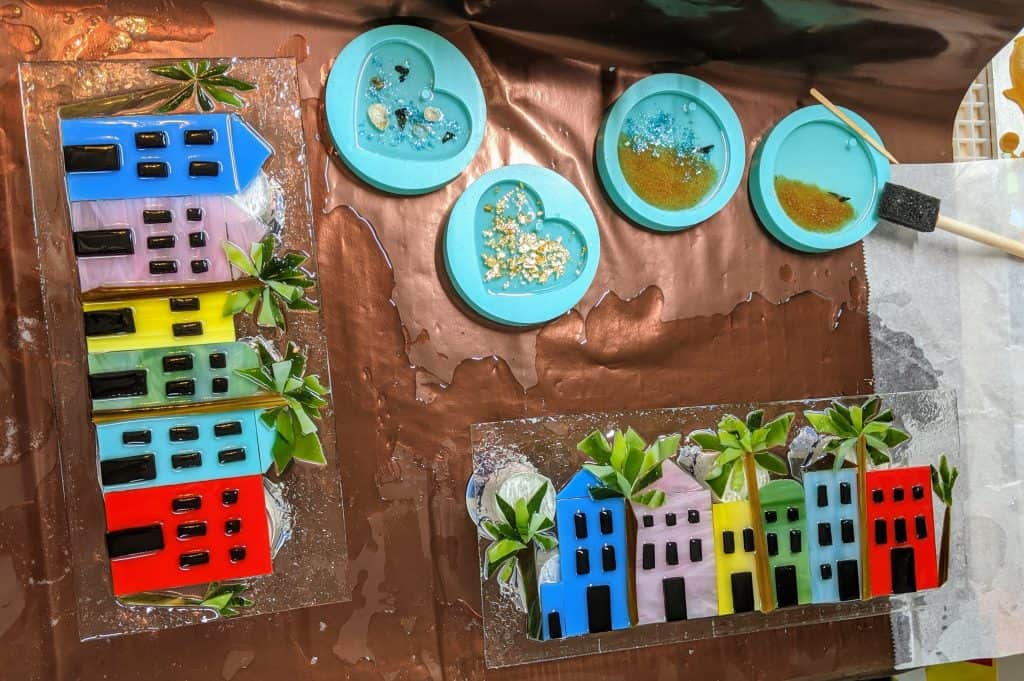
That’s why I put down paper on my work surface, though, so no worries on the mess! And the resin looks great – these two rainbow rows are ready to go a day later.
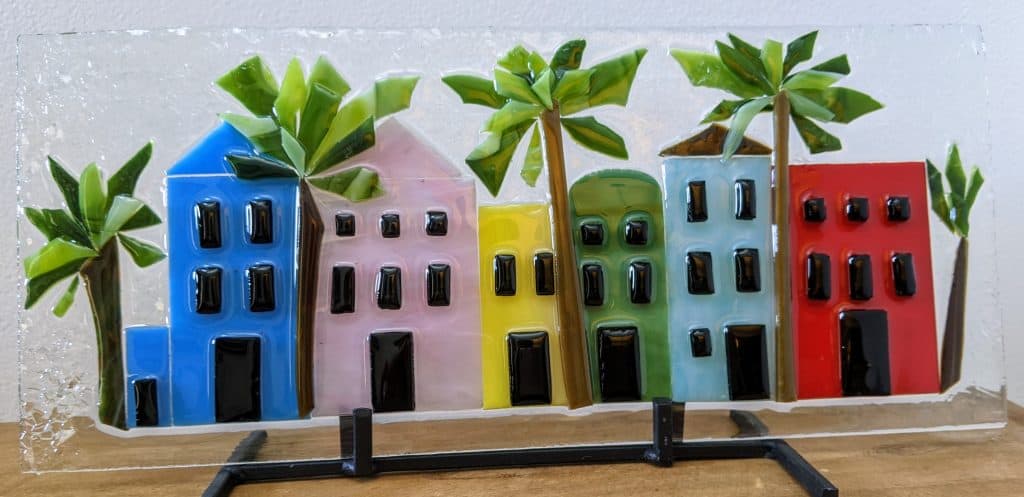
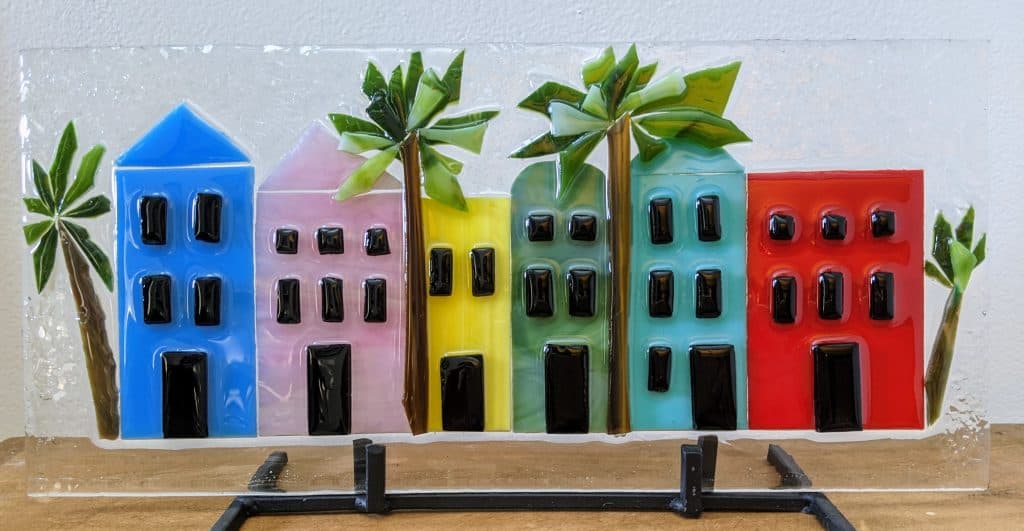