I actually started this last week, but forgot to take a picture. I decided to use up some of the mica I have left on a bigger project – a wavy rainbow window. I am starting in the middle with red and will spread out in waves from there.
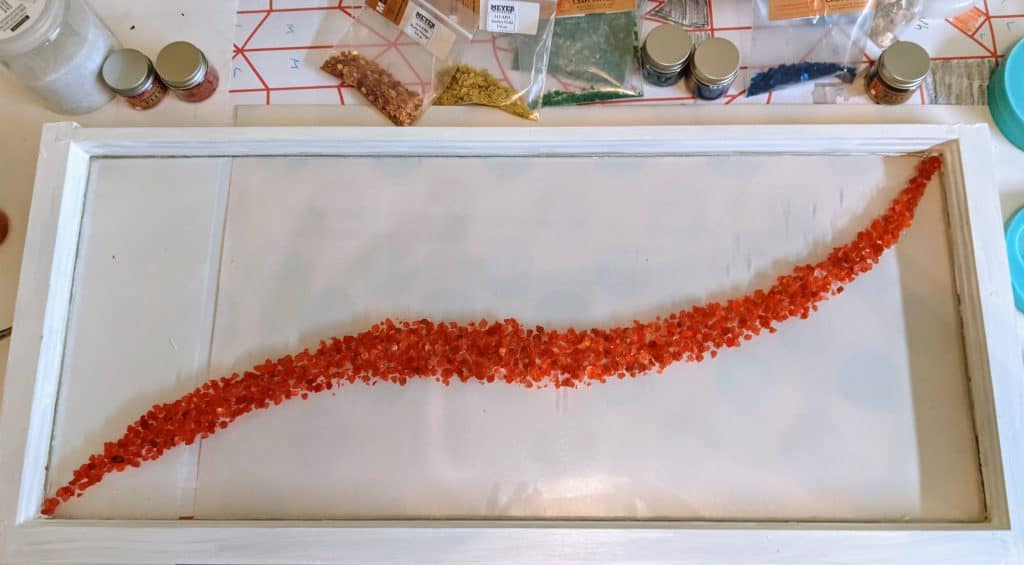
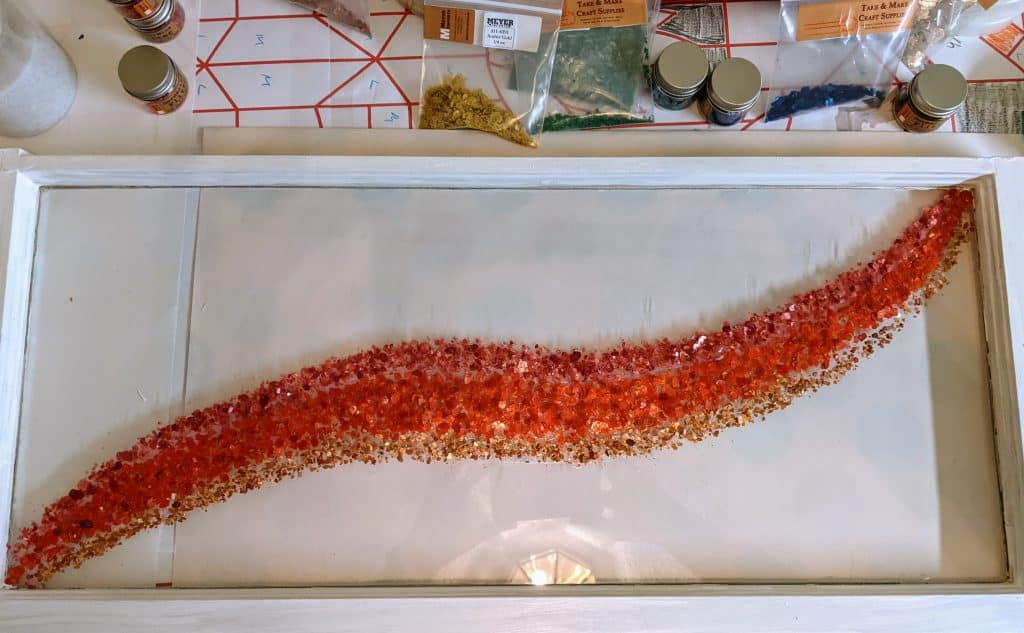
Glass of Sherry
Today is Thanksgiving, a great day to make some progress on small projects! Today was second layer of resin over the two heart / mica rainbow suncatchers / ornaments and also for the first mica rainbow coaster. I liked the first mica rainbow batch so much that I decided to make a round mica rainbow suncatcher / ornament and three more coasters to match the first. Next up will be the second layers on those. I also made a medium sized stained glass snowman suncatcher that will need another layer of resin and some decorations tomorrow.
I was able to pop out a few finished projects from yesterday’s batch, too!
Continuing to try and make some new things for the small, outdoor, masks required pop-up craft fair I signed up to do at 3 Matadors for December 5th.
First I needed some more snowballs for snowmen, as I used up all the ones I had on hand. Back to the old grinder so to speak. 🙂
Before I start mixing my resin, I lay out all of my projects and needed supplies. Today was the second layer of resin on the holly suncatcher and all five coasters, though one will be a new coaster design and the other four will be sandollars in the sand. I like to elevate the larger projects like the snowman panel so I can reach any drips that happen. I sometimes tape the underside edge, but forgot this today.
I’m trying out some new colors of mica for the rainbow projects. I think they will be really pretty!
Now everything just needs to sit overnight to cure.
Today I poured the second layer of resin on several small projects and then spent some time making several small snowmen. I am experimenting with some abstract red and green coasters too, though my son says his favorite is the holly leaf suncatcher. My current favorites are the little snowmen. This is as close as you can get to making snowmen here in Charleston, SC. It’s 80 degrees outside and it’s well into November!
To make the “snowballs” for their bodies, I use glass nippers to rough out a generally round shape, then I use my glass grinder to smooth the edges. My fingers are pretty sore after making so many snowmen in one day! After the “snowballs” are ready, I paint on their faces (on the tiny ones). I use glass for the detail on the faces of the larger snowmen. Since these tiny ones are destined to be in two sided ornaments, I painted both sides of their faces / buttons and the little birds that will perch on their stick arms.
I also cut some backer glass and glued the pieces of this “big” snowman in place. I will pour the resin and decorate it another day, after the mosaic adhesive has had a chance to fully cure. This piece will be table top sized as it’s slightly smaller than a standard sheet of paper.
Suncatchers / ornaments are between 3-3.5″ across. Handmade suncatchers are $20 each. Handmande coasters with stained glass are $50 for the set. Contact me for delivery / shipping options.
Working on some small, fun projects inspired by friends and holidays. Poured the second layer on these ornaments and the first layer of a set of cardinal coasters today.
I decided to rotate the large Frank Lloyd Wright window I have been working on, and upon closer inspection of the “far” side, I decided to pour another thin layer of resin to address a few coverage issues. Since I was doing that, I mixed some extra resin to finish off a couple of coasters I’ve been working on and made a few new ornaments using mica, glass, sand, shells etc. I still have to pour a second layer on the ornaments, but the coasters should be ready to pop out of their molds tomorrow. The picture isn’t very good, but hopefully I’ll get some better ones once these are out of their molds.
This afternoon I added a second layer of resin to the panel. Grr. It looks great overall, but the devil is in the details for me. The second layer had some issues. One issue was where the resin didn’t lay invisibly over the first layer. I tried to minimize that by blowing resin into the edges of the glass pieces. However, as bubbles formed, I tried to remove them with the heat gun. One spot in particular “lumped up” when I was doing this. I can repair it by filing down the lumpy parts and pouring a new layer over everything, but one goal was to preserve the texture of the glass I used for the petals of the lilies. If I pour another layer, the texture will be lost.
Two layers of resin
You can’t see it in the photos, but we’ll make a decision after everything cures.
Now that I have verified that my resin is OK, I prepared to pour the first layer of resin on the large Frank Lloyd Wright stained glass window project I’ve been working on since early August. I used some boards to elevate the window off of the table, then taped around the edge using a layer of painter’s tape and a second outer layer of duct tape.
My hope is that the painters tape will come off easily, while the duct tape will create a strong edge for the resin.
Once all the tape was in place and secure, I mixed 16 ounces of resin and poured it over the panel. I then used a sponge on a stick to distribute the resin as much as I could over the panel. I will have to repeat this with another layer later, as more resin will be needed to fill in all the gaps.
I then used my heat gun to further distribute the resin and remove bubbles that popped up while the resin settled. I spent about an hour and a half doing this.
Now I just need to wait overnight for the first layer to cure. After that, I will repeat with a second and hopefully final layer to fill in the remaining crevices.